WHAT IS SQF CERTIFICATION FOR DIETARY SUPPLEMENTS?
SQF (Safe Quality Food) Certification for dietary supplements is a comprehensive food safety and quality management certification designed to assure consumers and buyers that a product has been produced, processed, and handled according to the highest possible standards. The SQF Program is recognized by the Global Food Safety Initiative (GFSI) and covers all sectors of the food supply chain, including dietary supplements.
Food Safety Code: Dietary Supplement Manufacturing, Edition 9
SQF Dietary Supplement Manufacturing Code can be applied to food sector categories for dietary supplement manufacturing.
DIETARY SUPPLEMENTS AND AMAZON
Amazon’s updated Dietary Supplements Policy now imposes strict requirements on sellers, with non-compliance potentially leading to product listing removals, account suspensions, or even bans.
SQF certification offers several key benefits in this context:
- Ensure Compliance with Amazon’s Standards: The SQF Dietary Supplement Manufacturing Code is closely aligned with Amazon’s stringent requirements, making it easier for you to comply with their updated policies.
- Improve Product Safety and Quality: By adhering to SQF certification standards, your supplements are manufactured under rigorous safety and quality controls, minimizing the risk of product recalls and customer complaints.
- Build Customer Confidence: Earning SQF certification can enhance the trust of both trading partners and consumers, leading to increased sales and more positive reviews.
- Simplify Documentation and Audits: SQF certification provides thorough documentation, streamlining the process of submitting compliance evidence to Amazon.
KEY COMPONENTS OF SQF CERTIFICATION AND DIETARY SUPPLEMENTS:
The key components of SQF (Safe Quality Food) Certification for dietary supplements are designed to ensure that these products are manufactured, processed, and handled according to the highest standards of food safety and quality. Below are the primary components:
1. Food Safety Management System (FSMS):
- HACCP Implementation: The SQF certification requires a Hazard Analysis and Critical Control Points (HACCP) plan tailored to dietary supplements. This involves identifying potential hazards in the production process and implementing control measures to prevent contamination.
- Risk Management: Establishing procedures to identify, assess, and control risks to food safety and quality throughout the supply chain.
2. Good Manufacturing Practices (GMPs):
- Sanitation and Hygiene: Ensuring the cleanliness of the facility, equipment, and personnel to prevent contamination of dietary supplements.
- Personnel Practices: Training and maintaining hygiene standards for all personnel involved in the production process, including proper use of protective clothing and handwashing procedures.
3. Product Traceability:
- Supply Chain Management: Managing and monitoring all suppliers to ensure they comply with food safety and quality standards. This includes traceability of raw materials, ingredients, and packaging used in dietary supplements.
- Recall Procedures: Developing and implementing procedures for the quick and efficient recall of products in case of a safety issue.
4. Quality Management System (QMS):
- Product Specifications: Defining and controlling product specifications to ensure that dietary supplements meet the required standards consistently.
- Quality Assurance Testing: Implementing regular testing of dietary supplements to verify that they meet safety and quality standards.
5. Documentation and Record Keeping:
- Standard Operating Procedures (SOPs): Maintaining detailed SOPs for all processes involved in the production of dietary supplements, including manufacturing, packaging, and storage.
- Audit Trails: Keeping comprehensive records that document compliance with SQF standards and facilitate internal and external audits.
6. Internal Audits and Continuous Improvement:
- Internal Audits: Conducting regular internal audits to identify gaps in the food safety and quality management systems and to ensure ongoing compliance with SQF standards.
- Corrective Actions: Implementing corrective actions based on audit findings and continuously improving processes to enhance food safety and quality.
7. Labeling and Packaging Controls:
- Label Accuracy: Ensuring that product labels comply with regulatory requirements and accurately reflect the contents and nutritional information of the dietary supplements.
- Packaging Integrity: Verifying that packaging materials are suitable for dietary supplements, preventing contamination, and maintaining product quality during storage and distribution.
8. Regulatory Compliance:
- Adherence to Regulations: Ensuring that dietary supplements comply with all relevant regulatory requirements, such as those set by the U.S. Food and Drug Administration (FDA) or other relevant authorities.
- Regulatory Updates: Staying informed about changes in regulations and updating processes and procedures accordingly.
9. Supplier and Raw Material Control:
- Approved Supplier Program: Establishing a program to evaluate and approve suppliers based on their ability to meet SQF requirements for food safety and quality.
- Raw Material Testing: Implementing testing procedures for raw materials and ingredients to ensure they meet quality and safety standards before use in production.
10. Customer and Consumer Communication:
- Customer Feedback: Developing mechanisms for collecting and analyzing customer feedback related to the safety and quality of dietary supplements.
- Crisis Management: Preparing a crisis management plan to address any potential food safety or quality issues that may arise.
Summary:
These components form the foundation of SQF certification for dietary supplements, ensuring that products are produced under strict safety and quality controls, meet regulatory requirements, and maintain the trust of consumers and retailers.
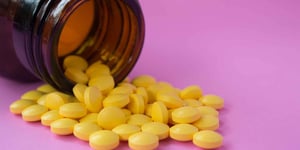
REQUEST A QUOTE FOR SQF CERTIFICATION FOR DIETARY SUPPLEMENTS:
Our team will review your request and provide a detailed quote tailored to your specific dietary supplement requirements.
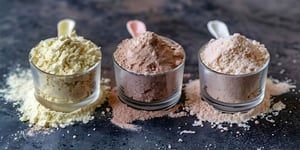
BENEFITS OF SQF CERTIFICATION FOR YOUR DIETARY SUPPLEMENT COMPANY:
Market Access: Essential for entering global markets and meeting buyer requirements, giving you a competitive edge.
Consumer Trust: Enhances brand reputation and assures customers of your product’s safety and quality.
Regulatory Compliance: Helps meet global standards and simplifies regulatory management.
Operational Efficiency: Streamlines processes, reduces risks, and cuts costs.
Continuous Improvement: Promotes ongoing development and employee engagement in maintaining high standards.
Supply Chain Control: Ensures better supplier management and product traceability.
Financial Benefits: Reduces costs, minimizes recalls, and attracts investment.
Global Recognition: Recognized by GFSI, boosting your brand’s credibility worldwide.
Customer Satisfaction: Consistent quality leads to higher satisfaction and stronger customer relationships.
THE PROCESS FOR IMPLEMENTING SQF CERTIFICATION TYPICALLY INVOLVES SEVERAL KEY STEPS:
-
Commitment and Leadership: Top management commits to implementing ISO 9001 and provides leadership throughout the process.
-
Initial Assessment: Conduct a gap analysis to assess current processes against ISO 9001 requirements and identify areas needing improvement.
-
Planning: Develop an implementation plan outlining goals, timelines, resource requirements, and responsibilities.
-
Documentation: Create or update documentation, including a Quality Manual, procedures, work instructions, and records required by ISO 9001.
-
Training and Awareness: Ensure employees understand ISO 9001 requirements through training and raise awareness across the organization.
-
Implementation: Implement the QMS across all relevant processes, ensuring procedures are followed and necessary changes are made.
-
Internal Audit: Conduct internal audits to assess QMS effectiveness and identify nonconformities.
-
Management Review: Review QMS performance with top management to ensure it meets objectives and identify opportunities for improvement.
-
Corrective Actions: Take corrective actions to address nonconformities and improve QMS effectiveness.
-
Certification Audit: Arrange for a certification audit by an accredited third-party certification body to assess conformity to ISO 9001 requirements.
-
Certification: Upon successful completion of the certification audit, receive ISO 9001 certification, demonstrating compliance with the standard.
-
Continuous Improvement: Maintain and continually improve the QMS through regular monitoring, measurement, analysis of data, and management review.
These steps provide a structured approach to achieving ISO 9001 certification and establishing a robust Quality Management System within your organization.
THE ASI DIFFERENCE
ASI can support your company in achieving SQF certification for dietary supplements through comprehensive services, including training programs, gap analysis to identify areas for improvement, consultation on implementation strategies, assistance with documentation development, conducting internal audits, and performing certification audits as an accredited certification body.
Our expertise will streamline your journey towards implementing a robust food safety and quality management system aligned with SQF standards, ensuring compliance and promoting continuous improvement within your organization.
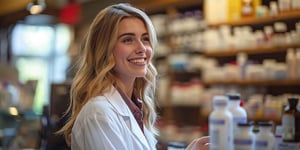
FREQUENTLY ASKED QUESTIONS:
1. What is SQF Certification?
SQF (Safe Quality Food) Certification is a globally recognized food safety and quality management system that ensures products are manufactured, processed, and handled according to the highest standards. It’s particularly important for dietary supplements, as it demonstrates compliance with stringent safety and quality controls.
2. Why is SQF Certification important for dietary supplement companies?
SQF Certification is critical for dietary supplement companies because it enhances market access, ensures compliance with global safety standards, builds consumer trust, and minimizes risks like recalls or regulatory penalties. Many retailers and distributors require SQF certification for their suppliers.
3. What are the key components of SQF Certification for dietary supplements?
Key components include the development of a Food Safety Management System (FSMS), Good Manufacturing Practices (GMPs), product traceability, rigorous documentation, internal audits, and continuous improvement processes.
4. How does SQF Certification differ from GMP Certification?
While both focus on safety and quality, GMP certification is often a regulatory requirement focused on manufacturing practices. SQF Certification is broader, covering the entire supply chain and integrating food safety and quality management, making it more comprehensive.
5. What are the steps to achieve SQF Certification for dietary supplements?
The steps include conducting a gap analysis, developing a food safety plan, documenting processes, training staff, implementing the plan, performing internal audits, addressing any gaps, and finally undergoing a certification audit by an accredited body.
6. How long does it take to get SQF Certified?
The timeline varies based on the company’s readiness and resources but typically takes several months. This includes time for preparation, implementation, internal audits, and the final certification audit.
7. What are the costs associated with SQF Certification?
Costs can vary widely depending on the size and complexity of your operation. Expenses include training, documentation, system implementation, and audit fees. It’s important to consider these costs as an investment in your company’s future.
8. Can SQF Certification help with Amazon’s updated dietary supplement policy?
Yes, SQF Certification aligns closely with Amazon’s updated requirements, making it easier for your products to comply with their policies, thereby reducing the risk of listing removals, account suspensions, or bans.
9. How often do we need to renew our SQF Certification?
SQF Certification is typically valid for one year. To maintain certification, companies must undergo an annual audit to demonstrate ongoing compliance with SQF standards.
10. What are the benefits of maintaining SQF Certification?
Maintaining SQF Certification helps ensure continuous improvement, enhances product safety and quality, boosts customer confidence, and keeps your company competitive in the marketplace.
11. Who conducts the SQF Certification audit?
The audit is conducted by an accredited SQF certification body, which sends a qualified auditor to assess your facility and processes against the SQF standards.
12. What happens if we fail the SQF Certification audit?
If you do not pass the audit, you will receive a report outlining non-conformities. You’ll need to address these issues and undergo a follow-up audit to achieve certification.