.jpg?width=300&name=Untitled%20design%20(6).jpg)
Your Trusted Partner for BRCGS Certification
With over 22,000 certified sites in more than 130 countries, BRCGS certification is accepted by 70% of the top 10 global retailers, 60% of the top 10 quick-service restaurants, and 50% of the top 25 manufacturers.
BRCGS CERTIFICATION
At ASI, we understand the significance of upholding the highest standards of quality and safety in the industries we serve. Our commitment to excellence is demonstrated through our adherence to BRCGS (Brand Reputation Compliance Global Standards) certification.
BRCGS CERTIFICATION:
BRCGS certification isn’t just a trust marker; it’s a sales catalyst. Certified businesses report an average 7.5% increase in sales, with 55% of companies stating they secured new customers as a direct result of certification. These new opportunities arise because certification makes businesses more appealing to buyers and distributors who prioritize quality and safety.

Request a Quote for BRCGS Certification:
Our team will review your request and provide a detailed quote tailored to your specific requirements. We look forward to assisting you in achieving BRCGS certification.
What is BRCGS Certification?
BRCGS (Brand Reputation through Compliance Global Standards) certification is a globally recognized food safety and quality certification designed to help businesses meet regulatory and customer requirements. It ensures that food, packaging, and consumer products are produced safely, legally, and with consistent quality.
Why is BRCGS Certification Important?
✔ Recognized by Major Retailers & Food Brands – Many supermarkets and food manufacturers require suppliers to be BRCGS certified.
✔ Ensures Compliance with Food Safety Laws – Helps businesses follow strict industry regulations and best practices.
✔ Builds Trust with Customers & Retailers – Demonstrates a strong commitment to food safety and quality.
✔ Reduces Business Risks – Minimizes the chances of recalls, contamination issues, and legal liabilities.
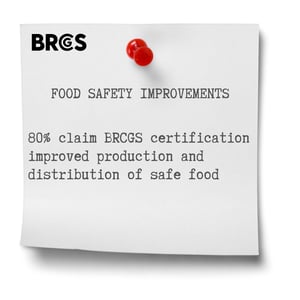
Who Needs BRCGS Certification?
BRCGS certification is ideal for businesses involved in:
✔ Food Manufacturing & Processing – Ensures food products meet the highest safety and quality standards.
✔ Packaging Production – Verifies safe and hygienic packaging for food and consumer goods.
✔ Storage & Distribution – Maintains food safety and product integrity during transportation and warehousing.
✔ Retail & Brand Owners – Ensures product safety throughout the supply chain.
Why Choose ASI for Your BRCGS Audit?
Choosing the right certification body for your BRCGS audit is crucial to ensuring compliance, efficiency, and a seamless certification process. At ASI, we specialize in providing fast, reliable, and cost-effective BRCGS audits to help your business meet food safety and quality standards.
✔ Expertise You Can Trust
Our highly experienced auditors have deep knowledge of BRCGS standards and industry regulations, ensuring a smooth and professional audit process. We offer personalized support to guide you through every step of certification.
✔ Fast Turnaround & Flexible Scheduling
We understand that certification is time-sensitive, which is why ASI provides quick scheduling and efficient audits to minimize disruption to your operations. If you need an audit urgently, we offer expedited services to help you meet retailer or customer deadlines.
✔ Cost-Effective Certification Solutions
Our competitive rates ensure that you receive high-quality certification services at a cost-effective price.
✔ Strong Industry Reputation
ASI is trusted by leading food manufacturers, processors, and packaging companies across North America. Our commitment to helping businesses achieve and maintain BRCGS certification has made us a reliable partner in the food safety industry.
✔ Ongoing Support & Guidance
Our team offers continuous insights, resources, and expert advice to help you maintain compliance beyond your initial certification. We also keep you informed about BRCGS updates and regulatory changes, so you’re always prepared.
BRCGS CERTIFICATION
Frequently Asked Questions
Have Question? We are here to help
What is BRCGS Certification?
BRCGS (Brand Reputation Compliance Global Standards) certification is a globally recognized standard that ensures the safety, quality, and legality of products, covering various industries like food production, packaging, and storage. Achieving BRCGS certification helps businesses meet regulatory requirements, reduce risks, and gain customer trust, ultimately enhancing market access and protecting brand reputation.
What are the main standards under BRCGS?
- Food Safety
- Packaging Materials
- Storage and Distribution
- Agents and Brokers
- Consumer Products
- Gluten-Free Certification Program
- Plant-Based Certification
How does BRCGS differ from other food safety standards like SQF or FSSC 22000?
While all these standards focus on food safety, BRCGS places a strong emphasis on product quality, safety, and legality, as well as supplier management and food safety culture. It also requires annual audits for recertification, whereas FSSC 22000 is based on ISO standards and has a three-year cycle with surveillance audits. SQF, another GFSI-recognized standard, integrates food quality standards more directly within its levels.
What happens if we fail an audit or identify non-conformities?
If an audit identifies non-conformities, the company must implement corrective actions within a specified timeframe to address the issues. Failure to correct major non-conformities can lead to suspension of certification. The certification body will often conduct a follow-up audit to verify that the issues have been resolved.
How long does it typically take to get certified, and what is the process?
The process generally takes 3-6 months, depending on the company’s readiness. It involves developing the necessary systems, conducting a gap analysis, implementing corrective actions, and preparing for the audit. After the audit, any non-conformities must be addressed before certification is granted.
What is a gap analysis for BRCGS?
- Reviewing Existing Systems: Evaluates current food safety procedures, documentation, and quality management systems.
- Identifying Non-Conformities: Highlights areas where current practices do not meet BRCGS requirements.
- Assessing Prerequisite Programs (PRPs): Checks foundational programs such as sanitation, pest control, and training for alignment with BRCGS standards.
- Evaluating Hazard Analysis and Critical Control Points (HACCP): Ensures that the company's hazard control measures are adequate and effective.
- Providing Corrective Action Recommendations: Offers guidance on how to address identified gaps and achieve compliance.
- Preparing for the Certification Audit: Helps the company strengthen its systems to meet BRCGS standards, increasing the chances of a successful certification.
A gap analysis serves as a roadmap for companies to improve their processes and achieve compliance with BRCGS requirements.
Can BRCGS certification apply to non-food products, like packaging or logistics?
Yes, BRCGS has standards for different sectors, including food safety, packaging materials, storage and distribution, consumer products, and retail. Certification can be applied to packaging materials and logistics providers, ensuring safety and quality throughout the supply chain.
What are the costs associated with BRCGS certification, including audits and corrective actions?
Costs can vary depending on the size and complexity of the organization. Expenses may include initial assessment fees, audit costs, corrective action implementation, training, and certification body fees. It’s also important to budget for annual audits to maintain certification.